Choose the Innovative Factory Automation Company
Factory Automation Products and Equipment
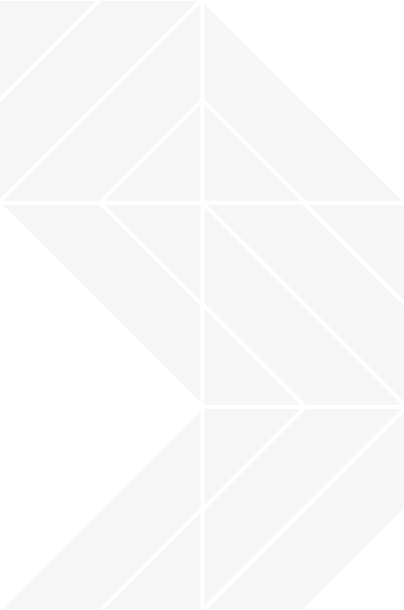
Pascal Engineering helps manufacturers automate processes to enhance productivity, reduce downtime, and improve worker safety. Our products support just-in-time production while increasing output for metal stamping, injection molding, and cnc machining. We strive to help businesses worldwide succeed through the continual innovation and improvement of our products and systems.