Die Setter: With Pascal’s die setter, vertical and horizontal positioning can be accomplished easily. It shortens setup time and improves productivity because adjustments can be made at the push of a button. There is also a model integrated with a clamp and die setter available.
Quick Mold Change System
Pascal Mold Changeover
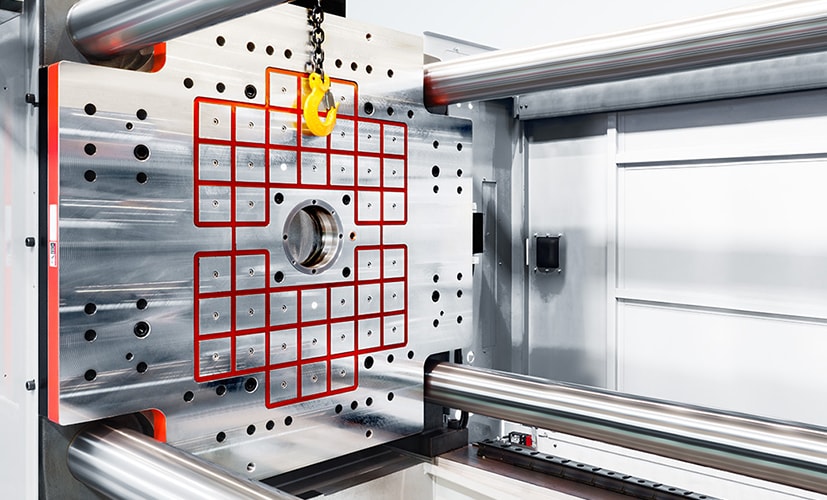
What is quick mold change in comparison to traditional mold changes?
Quick mold change is the process of switching out molds and dies automatically, a process often referred to as SMED, or single-minute exchange of dies. A quick mold change system is much faster than traditional methods and it can drastically reduce downtime and increase productivity while helping to keep the work environment safe.
With traditional mold change methods, the process can be extremely time consuming. Tools are necessary to bolt and unbolt the manual mold clamps, and often the operators must walk back and forth around the injection molding machine several times. Accidents can occur due to human error because there is no safety signal. The operator might forget to secure the manual clamps and as a result the mold could drop.
A quick mold change system is not only faster but it has an interlock system that ensures that the operator cannot proceed with the mold change until all the necessary conditions are met. The operator is kept safe because they will be alerted and cannot continue with the changeover if clamps are not properly secured.
Quick Mold Change System for Injection Molding Machines
Pascal offers a wide range of mold change options and mold clamps for two-color injection molding machines, vertical loading injection molding machines, as well as horizontal loading injection molding machines. We can configure a quick mold change system that will best suit your application based on your IMM machine type, tonnage, and the allotted space.
When you install a Pascal quick mold change system, hydraulic or pneumatic quick mold change clamps automatically and safely fasten and unfasten the mold from the injection molding machine. The mold is moved quickly and easily, and clamped into the right position with the pneumatic clamps every time. Once the material for the subsequent job is put into the machine and the mold quickly clamped, your next job is ready — in the shortest possible time.
Why is a quick mold clamping system needed?
Production lines are often required to make a relatively small quantity of parts in a short time so that orders can be delivered quickly. This requires just-in-time (JIT) manufacturing and the need for streamlined processes with a minimal amount of downtime. A quick mold changeover system with a magnetic clamp will ensure that injection molding operations remain safe and efficient, boosting productivity to meet JIT requirements.
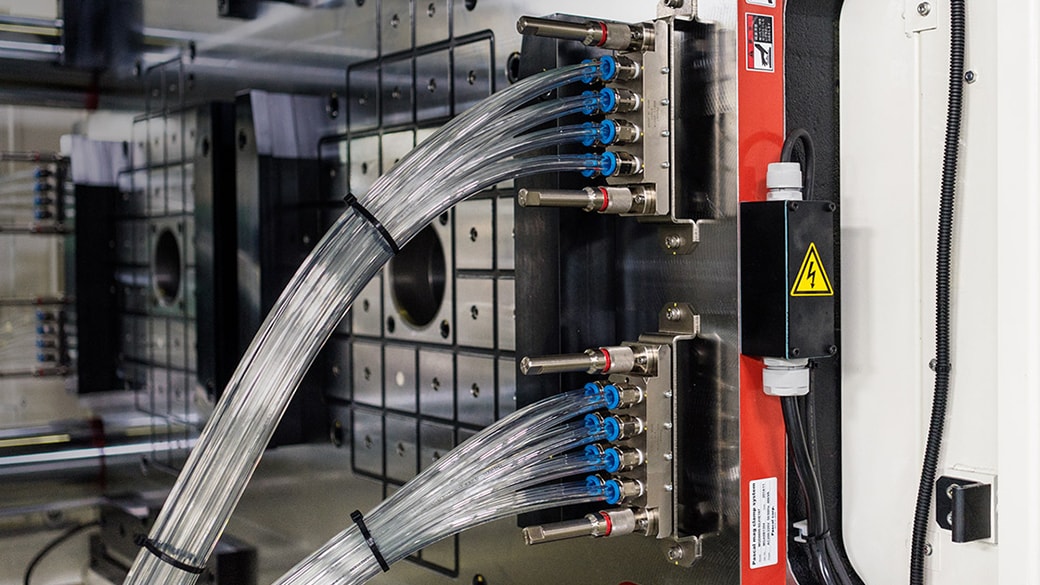
Reduce Downtime with Quick Mold Change System
Many of Pascal’s quick change mold clamps and other products are time savers that can help you to reduce downtime and increase productivity and safety.
Here is an example: If you can save at least 15 minutes on each mold change and you have 4 mold changes per day, that equals 22 hours a month. You would save 11 days per year! There is often much more than 15 minutes savings per quick changeover, so a quick mold change system could potentially gain you even more time!
There are many types of molding machine and mold tooling options for quick changeover. Pascal can evaluate your situation and requirements and develop the optimal automatic quick mold change system for your process and operation, using combinations of the mold changeover products listed below.
Magnetic Platen: A magnetic platen or magnetic clamp does not require any tools, and it clamps and unclamps at the push of a button in just 0.5-4.5 seconds.
Hydraulic/Air Clamps: A wide variety of mold clamps and die clamps are available including T-slot slidable types, long stroke types, t-slot less types, bolted types, and other automatic clamps with sensors in a variety of sizes and options.
Control system: This air-driven unit controls the hydraulic and air clamps. Most of our control systems are solenoid operated, with options ranging from small to large injection molding machines. An electric motor drive control for large IMMS is also available, along with non-leak valve units.
Mold/Die Changer: The next mold can be loaded onto a mold changer while the IMM is in operation, stopping operation only for a quick swap of the molds.
Automatic Coupler: An automatic coupler can connect multiple ports for hydraulics, water, and air all at once, saving time and guesswork.
Multi Coupler: The multi coupler is similar to the automatic coupler, except it is a manual option that can come with or without a check valve. It has ports for water, hydraulics, and air ranging from 4-12 ports.
Ejector Rods: Pascal’s magnetic Easy Ejector rods are lightweight and require no tools. For a 100 ton injection molding machine the time spent swapping ejector rods went from 1 minute and 6 seconds down to just 8 seconds!
Rotator: A mold rotator or mold flipper can safely rotate large molds and dies in seconds, and no one has to guide the mold with a crane.
Locating & Positioning Devices
Octagonal locate ring: Pascal’s highly rigid and durable locate ring provides high accuracy mold positioning for insert and hoop molding. It can help to improve mold set up time by connecting in seconds, and it eliminates the need to reteach robots. The locate ring is designed with 8 faces provide easy centering. Many options are available for vertical loading injection molding machines from 50 tons and upward.
Die Stopper: This is available as an alternative to the die fall protection hook. It prevents the die from falling due to the misplacement and nozzle touch of the ejector and ensures quick clamping.
Die Leveler: If working with a smaller mold and it cannot be modified for use with a die setter, then Pascal’s die leveler can assist. The process is streamlined with a leveler because the mold does not have to be inched into place with a crane. It can be used with molds up to a maximum of 2.5 tons.
Factory Automation Equipment and Systems
Pascal Engineering Inc. has spent decades helping manufacturers streamline and automate their manufacturing processes to support JIT production. Our industry experience ranges from automotive and industrial machinery to appliances and medical injection molding facilities.