Automated Solutions for Injection Molding Machines
Injection Mold Clamps & Automated Mold Change
Pascal’s Quick Mold Change (QMC) System utilizes automated mold clamps for injection molding to decrease non-productive changeover time in the plastics industry. Automated systems significantly reduce the downtime required for mold changes compared to conventional methods such as changing out the mold with a crane. With a quick mold change system including a magnetic clamp and a mold changer, the amount of time saved varies depending on the size of your injection molding machine. As one time-saving example, a magnet clamp brought 60 minutes down to just 15 minutes for mold installation on a 250 ton IMM, gaining 45 minutes more for production!
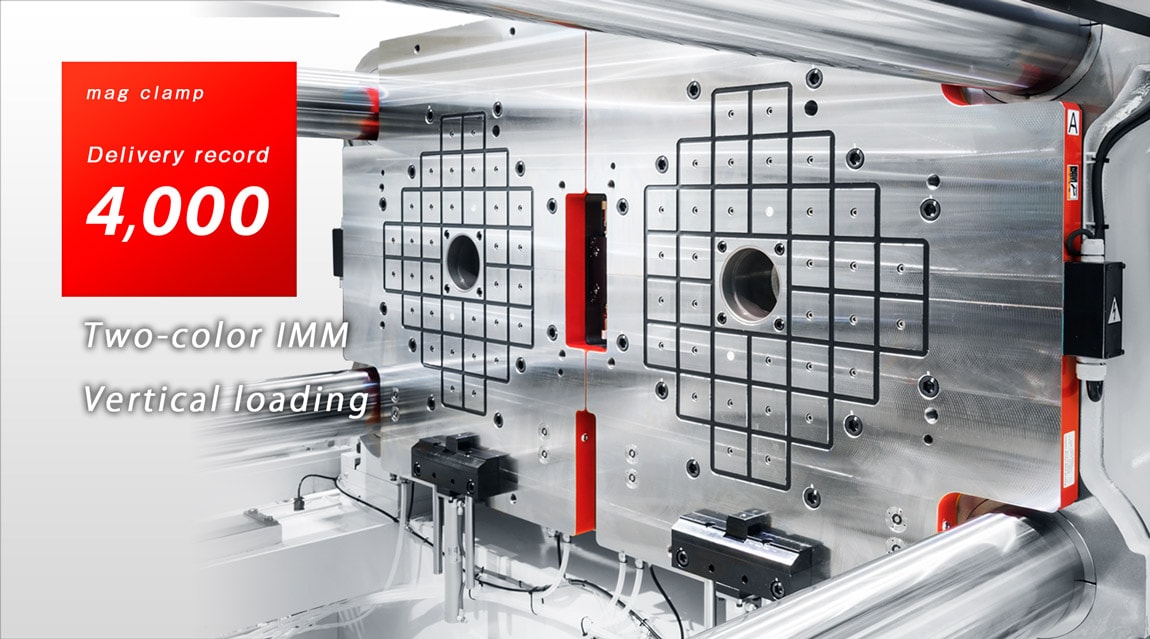
Benefits of Using Automation
Time Savings
Instead of manually loosening and tightening every clamp with bolts, which can be time consuming, the machine operator simply presses a button to release and secure the magnetic injection mold clamp.
Another time saver is a mold changer, because the operator does not have to precariously install and remove the mold with a crane. The crane can simply place the mold on the changer, and the changer will do the work, freeing up the crane for other operations. It saves time because this can be done while the injection molding machine is in operation, rather than halting production for the mold changeover. Less downtime means increased injection molding machine capacity for production.
In addition, we offer other time savers including automatic couplers that connect multiple ports at once, easy-change ejector rods that are magnetic and can be moved to a new position in seconds, and location devices such as die setters and levelers that are all unique and unrivaled in the market.
Smaller Runs
Because of the reduced time involved in changing molds, quick mold change equipment incorporating injection molding machine clamps provide the ability to run smaller batch sizes and operate shorter production runs — vital for just-in-time (JIT) manufacturing.
Improved Safety
Quick mold change system technology reduces worksite accidents with control and operation panels that provide safety interlock. Accidents due to human error such as forgetting to secure a clamp can be avoided. If the mold is not properly clamped, the job will not run until all clamps are in proper position.
Operators often endanger themselves by standing on top of the injection molding machine to attach hooks to the mold for crane removal. Footing in these places is often precarious and slippery with oil, and they risk a dangerous fall. With a mold changer, operators do not have to put themselves at risk climbing on top of the IMM, and the mold change takes place at the push of a button.
A rotator can help keep IMM operators safe, flipping the mold over without a crane which is often very dangerous for the person guiding the mold. The mold could sway dangerously, or it could be dropped on someone’s foot. Injuries can be avoided when turning the mold over by implementing a rotator that will automatically do the work.
Bottom Line Impact
Labor costs are reduced as a result of the time savings; fewer employees are required to change molds. The ability to run smaller batches reduces inventory costs. The overall increase in productivity translates into the ability to accept more jobs and grow revenue.
Pascal continues to grow business and adapt new technologies — all while working with leaders in the industry for plastic injection mold parts — so we can provide quality products and service to our customers.
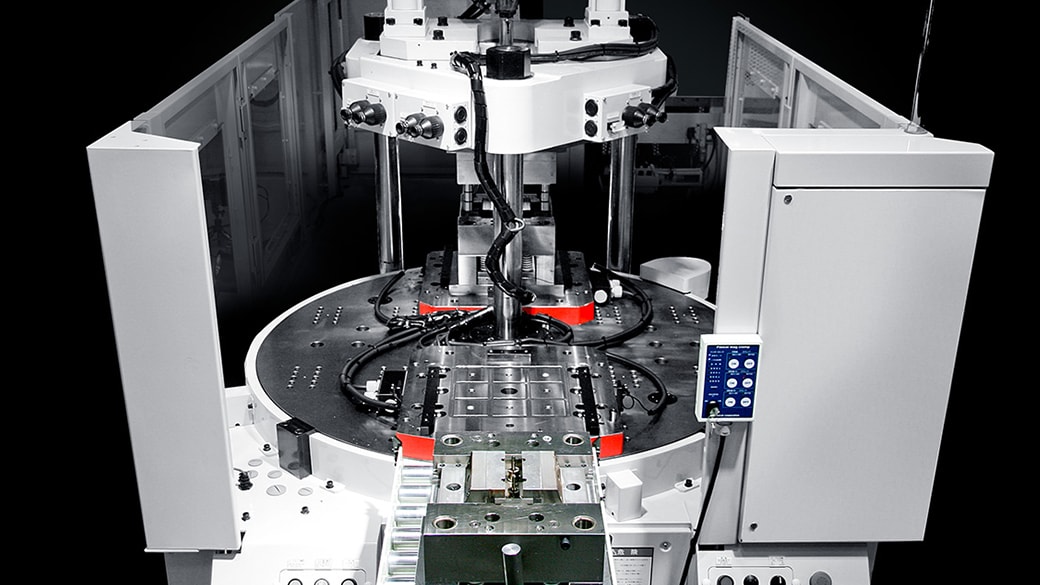
Options Based on Injection Molding Machine Type
Depending on your injection molding machine design and components, the injection molding machine loading type will determine the arrangement of the mold changer and clamping system:
- IMM vertical loading for machines in which the mold is set from the top by crane
- IMM horizontal loading for machines in which the mold is set from the operation or non-operation side
Pascal mold changing systems can be customized to suit your needs. They can be arranged for a large range of IMM tonnages, including automatic drive roller types, manual rail types, and horizontal loading mold carts to name a few.
Quick Changeover/Single-Minute Exchange of Dies (SMED) Process
Pascal Engineering has the expertise to help improve your injection molding machine process with a quick mold change system. This process of automating the mold change is often referred to as SMED, or single minute exchange of dies. We will evaluate your situation and develop an automatic mold-changing solution to help you shorten downtime, speed up production and ultimately increase profitability.

Mold Change for IMMs in Cleanrooms
Side loading mold carts: In some environments such as cleanrooms where space is limited, ceilings are low, and cranes won’t fit, a horizontally loading system with a mold cart might be necessary. A mold cart can save space because it can be used for multiple injection molding machines at once. Many possible configurations of varying sizes are available to best suit the needs of your space.
Utilization of a side load mold cart ensures less chance of operator injury because there is no tool work involved for mold changes. Mold carts are designed for the operator to be able to manually push molds in and out of machine with ease on carefully engineered and precisely machined roller systems.
ISO class environments: A magnetic clamp is suitable for ISO class 7 and 8 environments because since it operates with magnets rather than pneumatics and hydraulics which could potentially interfere with air particle requirements.